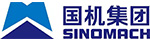
轴承套圈每个生产工序均会对其质量产生影响。轴承失效分析中,套圈的材料孔洞缺陷、锻造缺陷、热处理质量、磨削烧伤、环境腐蚀是导致轴承失效的主要原因,因此必须重视套圈的生产质量,减少轴承因套圈质量问题而导致的早期失效,最终实现提高轴承寿命的目的。
对废品分析轴承套圈产生缺陷的原因进行统计发现:材料因素是影响套圈质量的主要因素,包括材料内部冶金缺陷,如夹杂物、夹渣、显微孔隙,套圈因材料外部缺陷未完全清除的残留,如脱碳、微裂纹、表面缺陷等;其次为热处理工艺,包括热处理质量不合格(组织粗大,屈氏体不符合标准要求,粗大网状碳化物)和淬火应力裂纹;另外,磨削质量也是影响套圈质量的主要因素之一,主要为磨削烧伤引起表层组织改变,严重时产生磨削裂纹;管理因素(人为原因)主要是指套圈生产过程中操作不当引起的机械伤(划伤、垫伤)以及环境腐蚀(酸腐蚀和氧化腐蚀),提高操作人员的责任意识及业务水平可以预防此类缺陷的产生。
1、套圈常见质量问题及特征
1.1 材料质量缺陷
材料质量缺陷是决定轴承套圈质量的重要因素。套圈的材料主要有棒材和钢管。按照缺陷产生的部位,将材料质量缺陷分为内部缺陷和外部缺陷。
1.1.1 内部缺陷
内部缺陷主要有非金属夹杂物、夹渣、显微孔隙、发纹等。
非金属夹杂物是轴承钢冶炼过程产生的,无法避免,因此GB/T 18254—2016对轴承钢非金属夹杂物有特殊规定。非金属夹杂物存在于套圈基体内,成为裂纹源造成套圈早期剥落;加工过程中偶尔会裸露套圈表面,造成套圈报废。磨削滚道面的非金属夹杂物裸露形貌如图1所示。
图1 外圈沟道面非金属夹杂物残留电镜形貌
套圈存在肉眼可见的夹杂物即夹渣(主要成分为炉渣或耐火材料)时,易成为裂纹源,使套圈过早损坏甚至报废。外圈外径面的夹渣缺陷如图2所示。
(a) 外径面缺陷形貌
(b)缺陷电镜形貌
图2 外圈外径面夹渣缺陷
显微孔隙又称显微裂纹,金相观察其沿晶界分布并沿轧制方向伸展。产生原因主要有材料中心疏松或加热温度过高,钢坯心部的低熔点合金相熔融。若套圈中存在显微孔隙,会极大降低晶粒间的结合力,影响套圈的力学性能;严重的显微孔隙淬火时容易产生裂纹,若暴露至轴承零件表面则易产生黑点,降低防锈性能甚至导致轴承产生疲劳剥落。外圈显微孔隙金相图如图3所示。
图3 外圈显微孔隙金相形貌
发纹是一种存在于钢材表皮下层的细小裂纹缺陷。产生原因为钢锭中的皮下气泡或非金属夹杂物经轧制变形后,存在于材料表层且沿轧制方向断续分布,数量不等。若套圈存在发纹缺陷,易产生剥落掉块。
1.1.2 外部缺陷
外部缺陷主要有材料裂纹、脱碳、凹坑等。
材料裂纹存在于棒材表层一定深度下,折叠裂纹的特征是与表面呈一定角度,裂纹中一般有氧化皮存在,裂纹两侧有脱碳现象。若材料裂纹在套圈中残留必定引起质量问题。在套圈车削成形过程中,若材料裂纹缺陷没有完全车除,便会在套圈上残留,最终造成后续加工或装配或使用过程中开裂。内圈外径面钢管裂纹残留如图4所示。
图4 车削成形后内圈外径面钢管裂纹残留
材料表面脱碳,若是钢管,主要产生在外圈外径面及滚道面挡边处和内圈内、外径面,分别对应钢管的外径面和内径面;若是棒材,材料表面脱碳指钢材外表面。脱碳对套圈质量的影响与裂纹相似,一方面套圈淬火时易产生淬火应力裂纹;另一方面,脱碳区拉应力较大,受外力作用易开裂,因此,GB/T 1255—2014对轴承套圈表面脱碳层深度进行了严格的控制。外圈外径面残留钢管原始脱碳层如图5所示。
图5 外圈外径面残留钢管原始脱碳层
材料表面缺陷,如较深的锈蚀坑、压痕等,若车削成形时不能完全去除,亦会在套圈表面残留,影响其加工质量。
1.2 加工成形缺陷
套圈制造方式不同,其成形工艺不同。仅对工作中遇到的套圈成形缺陷问题进行分析。
1.2.1 锻造工艺
锻造是轴承套圈常见的加工工艺。锻造可以细化晶粒,改善网状碳化物,从而提高套圈性能。然而,若锻造工艺不当会产生锻造缺陷,影响套圈质量。如G95Cr18不锈轴承钢,锻造温度过高易产生孪晶组织,这是标准JB/T 1460—2011严格控制的。常见的锻造缺陷主要有锻造组织过热、过烧和锻造折叠裂纹。
锻造过热组织会沿晶界析出粗大而封闭的网状碳化物,严重的网状碳化物会破坏材料的连续性,使钢的力学性能降低,特别是冲击韧性,而且其在退火中保持不变,只能通过正火才能消除。
过烧组织晶粒粗大,晶界局部氧化或熔融,主要原因是加热温度过高或保温时间过长等。GCr15轴承钢锻造过烧产生的熔融孔洞形貌如图6所示。
图6 锻造过烧熔融孔洞形貌(×200)
锻造折叠裂纹是由于切料不齐、毛刺或操作不当等在套圈表面形成,其特征是裂纹一般与表面呈一定角度,裂纹两侧有严重的脱碳层。粗磨外圈折叠裂纹形貌如图7所示。
图7 外圈锻造折叠裂纹形貌
1.2.2 车削工艺
车削是轴承套圈成形的主要缺陷:一方面是不能完全清除材料表面缺陷,使套圈表面残留,进而影响套圈质量;另一方面是较深切尖锐的车刀纹极易产生应力集中甚至烧伤,在淬火时产生淬火应力开裂,装配时产生断裂。其主要产生于套圈油沟及滚道面挡边处。外圈滚道挡边的裂纹缺陷如图8所示,原因是挡边存在车削烧伤。
图8 外圈滚道面挡边车削缺陷(×500)
1.2.3 冷辗及串光工艺
冷辗成形也是轴承套圈常见的成形方式,冷辗工艺不当造成的套圈质量缺陷主要为冷辗裂纹。冷辗属于冷加工,材料延展性有限,若辗扩较大,易产生冷辗裂纹,另外,GCr15轴承钢由于存在碳化物带(碳化物偏析聚集),此处组织硬且脆,在变形过程中易拉裂。沿碳化物带分布的冷辗裂纹缺陷形貌如图9所示。
图9 沿碳化物带分布的冷辗裂纹形貌
串光是改变套圈表面粗糙度的一种方法,其工艺不当易造成薄壁套圈产生磕碰伤甚至掉块,如图10所示。
图10 串光工艺不当所致的挡边掉块
1.3 热处理缺陷
热处理(主要指淬、回火工艺)是实现轴承套圈高强韧性的重要工艺,对套圈质量的影响较大。统计数据表明,热处理质量缺陷约占套圈废品的22.55%。常见的热处理质量缺陷主要有脱碳、淬火应力裂纹、组织过热及屈氏体不合格。
热处理脱碳是指套圈淬回火过程中表层碳含量低于正常含量,可分为完全脱碳和脱贫碳。完全脱碳时套圈表层为铁素体组织,金相下呈白色;脱贫碳时该区域马氏体针相对基体较粗大,但均为马氏体组织。随着热处理设备的改进,套圈淬回火时主要产生脱贫碳现象,会极大降低套圈表层的耐磨性和耐疲劳性能,局部产生拉应力,是微裂纹源区。
严重的热处理脱碳会产生淬火应力裂纹,其特征是形状不规则,深浅不一,裂纹开口处多存在油污,金相观察裂纹两侧无脱碳现象。
套圈组织过热主要因加热温度过高或保温时间过长而产生粗大的马氏体针。
屈氏体不符合标准要求主要是指加热不足引起块状屈氏体或冷却不良形成针状屈氏体,宏观表现为局部软点即硬度不合格。外圈表面严重热处理脱碳组织形貌如图11所示,其在装配时开裂。
图11 外圈热处理脱碳组织形貌
1.4 磨削缺陷
磨削是轴承加工过程的关键工序,是实现套圈精度尺寸要求的重要加工工艺。根据统计结果,磨削质量缺陷主要指磨削烧伤、磨削裂纹及其他磨削缺陷。磨削烧伤指表层组织烧伤(高温回火),降低表面耐磨性;磨削裂纹导致套圈开裂,整批报废,经济和时间损失巨大。
轴承套圈磨削烧伤常见于滚道面、内外径面以及端面,其特征是内外径面及滚道面呈振纹状或斑块状,端面烧伤多呈斑块状。磨削烧伤冷酸洗后呈灰黑色,金相观察组织呈暗黑色。磨削烧伤冷酸洗组织形貌如图12所示。
图12 套圈磨削烧伤冷酸洗组织形貌
磨削裂纹多为龟裂状,深度较浅,金相观察裂纹两侧无脱碳现象。磨削裂纹常伴有严重的磨削烧伤,但磨削烧伤不一定产生磨削裂纹。套圈磨削过程中,其表层应力状态较复杂,磨削裂纹的产生是综合应力的结果,因此分析其产生原因时需综合考虑,尤其是磨削前各工序的加工质量,如车削质量、热处理变形等。外圈内径面热酸洗磨削裂纹形貌如图13所示。
1.5 装配质量缺陷
图13 外圈内径面热酸洗磨削裂纹形貌
装配质量缺陷包括人为因素导致的磕碰伤或挤压伤,装配工艺不当导致套圈局部受力较大,产生变形甚至断裂,套圈保管或操作不规范会引起腐蚀及异物污染等。除装配工艺不当外,装配质量缺陷多为人为因素,而这是可以避免的。装配过程中外圈局部掉块如图14所示。
图14 装配过程中外圈局部掉块形貌
1.6 管理因素
管理因素主要指套圈各加工工序过程中由于人为因素引起的套圈机械伤(挤压伤、磕碰伤、划伤)以及腐蚀现象(酸蚀和锈蚀),其中以套圈腐蚀最为常见,占套圈废品比例约为10%。腐蚀现象在套圈滚道面最为常见,其特征呈单一或者簇状点状缺陷(偶尔呈线状),严重时呈凹坑状;另外,轴承各个加工工序过程均有可能产生腐蚀现象。腐蚀现象虽受环境影响较大,但若操作规范完全可以避免。外圈滚道面点状腐蚀缺陷形貌如图15所示。
图15 外圈沟道面点状腐蚀缺陷形貌
2、预防措施
1)加强材料质量检验。根据统计分析,目前国内轴承钢质量主要存在的问题为表面缺陷,其次为非金属夹杂物。尤其注意与设计及车加工结合,车除多余的材料缺陷;同时,控制夹杂物尺寸,少数尺寸较大的夹杂物是应力集中点,易产生微裂纹,若分布在表面则造成套圈废品或早期损坏;最后,碳化物不均匀性会影响套圈的热处理质量,造成力学性能不均,也会影响后续磨削加工(如热处理变形磨削时易产生磨削烧伤)。通过加强材料检验,从源头减少轴承套圈产生质量问题的概率。
2)优化轴承套圈加工成形工艺。优化热处理工艺,减少套圈产生组织过热或欠热以及脱碳现象,尽量避免淬火应力裂纹产生。优化车削工艺,避免产生尖锐的车刀纹以及尖角毛刺等。同时,根据套圈尺寸要求,尽可能多地车除材料原始缺陷。优化磨削工艺,避免产生磨削烧伤和磨削裂纹。
轴研所公众号 轴承杂志社公众号
营销热线
0379-64367521
0379-64880626
13693806700
0379-64886322
0379-64881181