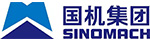
轴承磨削加工包含磨削、超精、研磨等,下面将重点介绍关于轴承磨削、超精加工的一些技术及特点。
1 轴承的磨削、超精加工工序
普通球轴承外圈与内圈的磨削、超精加工工序实例如图1所示。
图1 球轴承的磨削、超精加工工序实例
经塑性加工及切削加工,完成成形加工的工件,实施热处理之后,首先,用双端面磨床磨削基准端面。然后用纵向进给贯穿无心磨床磨削外圈外径面,可连续加工。之后,以外圈端面外径面为基准,进行外圈沟道磨削和超精。同样,内圈要进行内沟磨削、内径面磨削、内沟超精。然后提交给装配、检查工序。
1.1 平面磨削
用双端面磨床磨削内、外圈的两端面。双端面磨削是按规定的间隔、正确校准并装配两块砂轮,使套圈通过两砂轮之间,以规定的尺寸与平行度精磨两端面,能实现连续的高效率加工。
1.2 纵向进给贯穿无心磨
用纵向进给贯穿无心磨床磨削外圈外径。其方法为:无心磨床导轮、托板和砂轮3点支承外圈,导轮旋转外圈,砂轮旋转进行磨削。由于并不具备如卡盘加工一样的工件旋转中心,所以称为无心磨削,其结构如图2所示。
图2 纵向进给贯穿无心磨
通过正确设置磨削点、托板支承点及导轮支承点的角度,以支承磨削面进行加工。开始加工时,形成粗磨的精度,逐步地修正外圈外径圆度,最终确保外圈足够的圆度。此外,使导轮倾斜,沿工件轴向进给,能实现连续高效率加工。
1.3 支承块无心磨削
图3为支承块无心磨削示意图。用支承块分别支承已在磨削中的外径面或内沟,用电磁力将端面吸附到称为支承板的夹具上,在主轴旋转驱动的状态下磨削外沟或内径面。主轴中心与用支承块支承的工件(外圈)中产生偏心,利用由于偏心与旋转产生的推压力,工件稳定地在支承块上旋转。外径与外沟可按恒定壁厚加工,能够得到规定的沟与外径的同心度与沟圆度。
图3 外沟的支承块式无心磨削
为实现圆弧状的R形沟,要将砂轮成形为R形状(砂轮修整),复制并加工出该形状。R形修整中,有以下方法:复制预先制作出了其R形状的成形滚动式砂轮修整器形状;与旋转单一金刚石修整工具进行修整的方法。
内沟也是支承块式无心磨削,而该工序用支承块支承被磨削的沟进行磨削。因为用支承块支承磨削面,并不像前述的外沟磨削那样,已处在成为圆度基准面上,用该工序加工出新的圆度。为范成加工。该圆度的范成机理与外圈的无心磨削一样,无心前托块与后支块相当于无心磨床的托板与导轮。
1.4 超精加工
图4为球轴承的超精加工示意图。超精加工是将粒度细小的油石压在旋转的工件上(如内、外圈),与工件旋转呈直角方向上给予微小的摆动,精加工工件表面。至于球轴承沟道的超精加工,是以沟R中心为油石摆动中心,进行加工。此外,开始时,使用适应于工件形状的油石,由于并不实施油石的修整,利用由于油石磨耗导致的油石自锐作用,一边维持油石形状,一边持续进行加工。
图4 球轴承的超精加工
超精加工表面为镜面,由于凹凸少,油膜破裂难,所以具有以下特性:耐磨性、耐蚀性优异;由于产生的加工热量小,加工变质层很薄,故承载能力高;与断续式切削加工痕迹的磨削面不同,由于形成连续的切削加工痕迹,产品静音性能好。
2 轴承加工技术方向
2.1 应对难切削材料的加工技术
从磨削特性来看,高功能的新材料基本上属于难切削材料,产生加工效率差,砂轮锐度维持难的问题。作为适应于难切削材料的磨削技术,首先提及的是扩大CBN砂轮的应用范围。CBN砂轮的磨粒硬度与锋利度、寿命优于传统的氧化铝砂轮,适合于难切削材料,但有修整性能及价格上(高)的问题,不过其应用范围在逐步扩大。
2.2 应对环境问题的加工技术
作为一项与环境协调的磨削加工技术是开发加工冷却润滑液(冷却液)。冷却液被用于加工部位的润滑、冷却、清洗,磨削加工的多数情况下是加工时产生热量,根据表面精度质量的要求,需大量使用冷却液。正在开发的技术是用必要的最少量的冷却液进行磨削加工,以及利用雾滴及油雾冷却的加工技术。
为了削减CO2排放,首先采取的对策是提高磨床及超精加工机床的能源效率。但是,作为加工技术,如从去除加工所需的能源来看,磨削比车削需要更多的能源。因此,有必要通过削减磨削加工余量或硬车,以削减磨削的负荷,在整个工序上实现节能。
2.3 应对高精度化的加工技术
提高机床主轴轴承的旋转精度,对电机轴承的振动、静音性等要求越来越高。
为提高轴承的旋转精度,通过磨削设备的低振动、高精度化,优化磨削条件,排除磨削状态的干扰,以提高圆度,应使用亚微米级圆度的主轴轴承。
为实现轴承的低振动、静音化,改善滚动体滚动面的超精加工质量,有利于大大提高表面粗糙度与圆度等。
2.4 应对低成本化的加工技术
对轴承的磨削技术也在提出低成本化要求。因此,提高自动生产线的产量,开发低价格的生产线设备,生产线运转的省人化、无人化技术是必要的。
要提高产量,必须压缩循环时间,提高设备运转率。为缩短作业周期,必须开发能压缩上料等空转时间的设备,开发提高磨削效率的技术。
为提高磨削效率,使用CBN砂轮、陶瓷砂轮的实例在增加,这类砂轮具备超过传统的氧化铝砂轮的磨粒强度与锋利度。即便在超精加工工序中,也在通过砂轮的开发,确保削减磨削加工余量,谋求压缩加工时间。
此外,为同时兼顾提高磨削效率与高精度化,有必要实现磨削设备的高刚度化、低振动、高精度化,通过功能的集中与重新评价设备的制造工艺,开发能同时兼顾低成本及高效率、高精度化的设备。
在省人化、无人化操作系统方面,正在进行的开发是,对于过去用人力实施的加工状态的监测、金刚石磨具磨耗及机械的热变形,不通过人力,能自动地处理尺寸调整,交换磨具及设备异常时的处置等的系统。
2.5 适应于多品种少批量生产的加工技术
作为应对装置(装备)的更换方式,以包括在自动化生产线上的搬送在内的夹具、工具及修整装置的交换,容易提高精度为目标,正在开发在以上诸多方面做了精心考虑的加工设备与生产线。
3 小结
轴承磨削加工的环境随着加工要求条件的不同也会产生巨大变化,但是高功能、高精度、低成本是轴承磨削加工永恒的课题,有利于环保也是非常重要的课题。
(来源:轴承杂志社)
轴研所公众号 轴承杂志社公众号
营销热线
0379-64367521
0379-64880626
13693806700
0379-64880057
0379-64881181