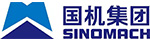
提高轴承疲劳寿命从而提高资源利用率的一种方式是改善表面和次表面的特性。由文献可知承受滚压应力的部件中残余应力对部件疲劳寿命产生的影响。最大载荷所引起的剪切应力深度中的残余应力可持续提高轴承疲劳寿命。Voskamp在增加载荷的条件下进行了跑合阶段的轴承试验,并在更具普遍性的载荷下持续进行了试验。由于轴承在跑合阶段产生了残余应力,因此对轴承疲劳寿命产生了积极的影响。结果表明,装有经上述短期增加载荷跑合阶段而产生残余应力的内圈的深沟球轴承的疲劳寿命比未经跑合阶段的轴承套圈提高了3倍。市场上的轴承大多通过磨削和超精工艺加工而成,这种生产方法产量高且加工表面质量好,并且会产生最深20 μm的残余应力。与此相对,采用硬车与深滚压相结合的生产方法可在载荷引起的最大应力深度处产生残余应力,同时获得与磨削和超精后相当的表面粗糙度。
提高轴承疲劳寿命的第一步是开展标准轴承次表面区域的变化研究。接下来,开发和测试硬车与深滚压相结合的制造工艺来确定如何具体调整表面和次表面的特性。建立一种根据轴承预残余应力来计算轴承疲劳寿命的模型。最后,在四轴承试验台上对采用新工艺加工生产的轴承进行验证。
1、试验技术
使用Hembrug Microturn 100车床对NU206圆柱滚子轴承内圈进行硬车。该轴承材料为100Cr6钢,经淬火和回火后硬度为62 HRC。采用型号为DNMA150616的硬质合金刀作为硬车刀具,通过刷涂和磨削来调整切削刃的微观几何形状。这些工具由制造商提供,具有传统的Al2O3+Ti(C,N)涂层。深滚压工艺则采用静压滚压工具进行加工。
轴承在四轴承试验台上进行运行试验。一方面,所谓的筛选试验用于记录边界区域特性随试验时间的变化,并确定合适的表面和边界区域特性。另一方面,进行疲劳试验的统计。纯径向载荷下在试验台,上同时运行4套试验轴承,且每套轴承承受相同的载荷。该试验台配有润滑油温控功能,可实现对试验轴承润滑油温度精确控制。试验过程中采用黏度η40为68 mm2/s(η100为8.9 mm2/s)的全合成润滑油。设定转速n为4050 r/min,油温为60 ℃。试验时比油膜厚度λ不小于3来保证轴承为全油膜润滑。通过振动信号监测轴承的剥落损伤,只要监测到损伤就立刻停止试验。选择C/P为4的径向载荷,此时轴承上产生的Hertz应力pmax为2500 MPa。轴承疲劳寿命试验采用突然死亡法进行。
2、硬车-滚压工艺生产圆柱滚子轴承
如Denkena等人所示,由于车削和深滚压在工艺控制上具有相似性,因此可很好地结合。滚压球在表面的精确定位更有利于滚道表面形貌的精确加工,因此该工艺适用于制造滚动轴承。图1a所示的概念已被开发用于内圈的加工。加工刀具如图1b所示。为确保滚压球在进给方向的旋转沟道内的定位,球径(dk为3.175 mm)与刀片的转角半径(r为1.6 mm) 应相匹配。球的定位采用楔形导轨,保证定位精度为±2 μm。
图1 硬车-滚压复合工艺工具
硬车工艺无法在保证表面粗糙度的同时获得较好的内应力。加工过程中,表面粗糙度由进给速度和切削刃半径决定,切削刃半径过大会降低其表面粗糙度,同时会在z达300 μm的深度处产生大的残余应力。
通过深滚压工艺可有效降低表面粗糙度,同时获得大的残余压应力。进给速度和覆盖率u对硬车和车削-滚压过程中表面粗糙度的影响如图2所示。表面加工质量仅受覆盖率u的影响。引入过程控制变量Nw作为偏移因子来描述球在表面上的位置。这里Nw为进给方向位移χf与进给量f之比。残余应力的影响原理与Hertz接触应力相似。残余应力的穿透深度随着球尺寸的增大而增大。滚压应力影响残余压应力的大小。密合度的增加可使深滚压工具与相同表面积之间有更多接触。对于这2种工艺过程之间的相互影响,仅需考虑表面粗糙度即可。硬车工艺对表面粗糙度有重要的影响,这是由于高材料硬度阻止粗糙峰在滚压过程中完全变形,因此初始表面粗糙度也决定了最终表面质量。深滚压工艺主要影响残余应力状态。为了研究滚压过程中工件温度对边界特性的影响,在不同的工件温度下进行了试验研究。环境温度从室温升高至300 ℃。结果表明,随着温度升高,残余压应力的增幅最小,并且当温度超过200 ℃时,整个工件的硬度降低。然而,在硬车过程中产生的热量仅对工件局部产生影响。
图2 进给速度和覆盖率u对后续硬车和车削-滚压过程中获得的表面粗糙度的影响
3、提高轴承疲劳寿命的次表面区域设计
为了量化残余应力对轴承疲劳寿命的影响,建立了轴承内圈有限元模型,通过将外载荷和附加残余应力状态叠加来分析滚道表面下的三维应力状态。该模型可输出von Mises等效应力、正交剪切应力和静压应力,以便采用基于loannides和Harris的方法进一步进行疲劳计算。
外部载荷施加在轴承套圈上产生三维Hertz应力。该模型考虑了轴承滚道的真实轮廓,利用该模型可获得疲劳极限应力τu和疲劳应力指标τi,并将其作为loannides-Harris疲劳寿命模型的输人。根据loannides等人的研究,存活概率S确定为
该概念考虑了应力体积V中载荷引起的应力的大小和深度。根据文献,对于线接触,e为9/8,c为31/3 (Lundberg 和Palmgren的指数),h为7/3。使用Dang Van 指标作为应力相关的疲劳指标τi。该模型的计算结果与试验结果进行了对比,可在考虑残余应力的情况下计算轴承疲劳寿命。
4、圆柱滚子轴承的寿命评估
第一步将标准研磨的轴承作为参考进行研究。在试验滚动轴承的前3x107r(t为120 h)内,其表面和次表面的特性发生了显著变化。研究表明,对于研磨的轴承,残余粗糙峰发生塑性变形,产生残余应力。如Voskamp的研究所示,残余应力产生在最大剪切应力的深度处,且其应力值在轴承经历3x107r后保持恒定。
硬车轴承套圈的首次疲劳试验已表明这一工艺的潜在极限值。套圈的表面粗糙度过大会引起轴承过早失效,而表面粗糙度足够低的轴承与研磨的轴承试验结果相当。在疲劳寿命试验的跑合阶段,粗糙峰减小,残余应力增大。与标准轴承相比,由于自制轴承的工作表面没有凸度,会产生较低的最大Hertz应力pmax(2 300 MPa),因此,在试验过程中使轴承产生了较低的残余应力。
随后的深滚压工艺使滚道产生较高的残余应力并降低了表面粗糙度。在最初的3 x107r内,残余应力仍保持在较高的水平。与跑合阶段相比,该加工工艺使轴承产生更大的残余应力,降低了轴承运行期间的临界剪切应力,并可计算出提高的轴承疲劳寿命。这同样适用于硬车轴承套圈。硬车试样中的残余应力相较于车削后深滚压试样移动到更深的深度,如图3所示,在经过t为50 h和120 h的试验时间后,硬车试样的残余应力未发生显著变化。
图3 深滚压轴承和车削-滚压轴承的残余应力变化
轴承在进行了耐久性试验后考虑到接触应力略有不同。研磨的轴承的额定寿命L10为274h,Weibull斜率值为0.6;硬车轴承的额定寿命L10为771 h;硬车随后进行深滚压的轴承的额定寿命L10为1 924 h,相对于硬车工艺提高了2.5倍。研磨、硬车和随后深滚压加工的轴承的存活概率的理论计算与试验值的对比如图4a所示。
图4 不同工艺制造的圆柱滚子轴承的预期寿命
由于产生残余应力而使轴承疲劳寿命提高,残余应力几乎在载荷引起的临界应力深度处达到最大值。根据已验证的模型,深滚压和其他3种不同方式车削-滚压轴承套圈的计算轴承额定寿命L10,mod如图4b所示。在工艺设置时根据钢球尺寸(dk为3.175 mm[HG3]和6.35 mm[HG6])和切削速度vc而异。根据计算结果可见,经过车削-滚压工艺可使轴承具有产生足够的残余应力状态的可能性。
5、结论
由于滚动轴承在提高部件资源利用率中占有重要作用,本研究以圆柱滚子轴承为研究对象。目的是通过采用新的硬加工工艺来设计和调整轴承滚道表面和次表面的特性,并针对不同硬加工工艺的应用开展了相应的分析。考虑了次表面残余应力的影响,建立了在完全弹流润滑区域工作的圆柱滚子轴承的寿命模型。在此基础上,介绍了一种新的车削-滚压复合工艺,即硬车与深滚压同步进行的复合工艺。对采用硬车、硬车后深滚压和车削-滚压复合3种工艺制造的轴承内圈进行了评估。一方面考察了边界区域特性的变化,另一方面考察了轴承疲劳寿命。研究表明,在轴承设计中如果考虑表面特性和次表面残余应力,可显著提高轴承疲劳寿命。硬车和深滚压复合制造工艺已被证明是一种可产生有益的残余应力状态的生产工艺,可使轴承疲劳寿命提高2.5倍,生产效率提高1.4倍。在设计轴承时考虑到这点有助于提高资源利用率。
(参考文献略)
(来源:轴承杂志社)
轴研所公众号 轴承杂志社公众号
营销热线
0379-64367521
0379-64880626
13693806700
0379-64880057
0379-64881181