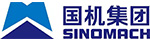
5 盾构机主轴承
5.1 轴承类型
盾构机是集机械、电气、液压、光学、力学、气动、传感、信息、导向为一体,能够完成掘进、支护、出渣等施工工序并进行连续作业的工厂化流水线式作业的隧道施工装备,被誉为“工程机械之王”,是衡量一个国家装备制造业水平的重大关键装备。随着我国城市地铁、铁路隧道、公路隧道、水利工程、城市市政燃气管道工程、排污管道工程、供热供冷管道工程、电缆管道工程盾构法施工的全面铺开,盾构机市场总需求呈快速增长趋势,也给盾构机轴承带来广阔的市场。
刀盘是盾构机的关键部件,在隧道掘进过程中发挥着重要作用。刀盘系统中的主轴承是传递掘进动力和运动的核心零件,在工作中承受着巨大的轴向力、倾覆力矩和一定的径向力,其性能、寿命和可靠性直接影响盾构机的施工进度、安全和掘进里程。小尺寸盾构机主轴承通常采用四点接触球和交叉圆柱滚子结构,个别有双列圆锥滚子结构。量大面广的盾构机主轴承主要有三排三列圆柱滚子组合轴承和三排四列圆柱滚子组合轴承,其中最常用的三排三列圆柱滚子组合轴承可分为内齿式(图13)和外齿式(图14)。
图13 土压平衡盾构机内齿式主轴承
Fig.13 Inner tooth main bearing for earth pressure balance shield machine
图14 泥水平衡盾构机外齿式主轴承
Fig.14 Outer tooth main bearing for mud-water balanced shield machine
盾构机主轴承的功能主要是支承及传递运动与载荷,然而由于盾构机转速极低,载荷极大且不可准确预测,可靠性要求极高,使盾构机主轴承承担着极大的风险,也对其设计制造提出了苛刻的要求。由于地质结构的不均匀性,盾构机掘进阻力的大小、方向可能剧烈变化,盾构机主轴承常常工作在冲击、偏载等极端工况下,对轴承的材料和热处理、结构、刚度、强度、寿命和可靠性等技术指标要求严苛。另外,还要求盾构机主轴承安装部位有可靠的密封,轴承内部有良好的润滑,相关密封结构和润滑剂均需特殊设计以满足苛刻的环境工况。
5.2 技术指标和关键技术
盾构机主轴承的主要技术指标为:无故障使用
10 000h(或累计掘进10 km以上),轴向跳动不大于0.1 mm,使用转速1~3 r/min。
5.2.1 设计技术
1)建立覆盖典型地质条件的工况数据库,制定满足静强度分析、动力学分析、可靠度预测、性能和寿命试验所必需的定常和非定常动态载荷谱、特殊工况下的极限载荷谱等。
2)完成盾构机主轴承失效数据搜集和分析,编制典型工况条件下的失效图谱。
3)开展低速、重载、冲击条件下盾构机主轴承的润滑理论及摩擦学研究,定常和非定常动态工况下主轴承的接触力学和动力学特征研究并形成相应的设计理论。
4)进行盾构机主轴承可靠性理论研究,建立不同地质和掘进工况条件下主轴承的可靠性理论与剩余寿命预估技术。
5)开展盾构机主轴承强度、刚度及寿命设计理论研究,主参数、滚子和滚道的理想凸度、轴承游隙、密封结构、保持架等零件结构参数的优化设计,以及性能仿真与寿命预测软件的开发。
5.2.2 控形控性制造技术
1)制定盾构机主轴承专用的钢材质量控制标准,建立钢材质量控制系统,实现“四化”要求,即成份设计智能化、内在质量高纯化、生产过程自动化和冶金质量一致化。
2)开展精密热处理技术研究,开发3个滚道同时淬火的无软带热处理工艺和齿轮淬火工艺,研制专用数控热处理设备和工装,提高淬火质量的一致性和稳定性;开发具有自主知识产权的材料性能模拟软件,动态在线控制及检测技术和表面改性技术。
3)全面掌握盾构机主轴承零件精密加工技术,开发滚道硬车工艺、CBN等超硬刀具制造技术。
4)全面掌握盾构机主轴承润滑与密封系统的设计制造技术。
5)全面掌握盾构机主轴承再制造技术,制定主轴承再制造质量标准。
5.2.3 质量控制与健康状态监控技术
1)制定盾构机主轴承产品标准,严格规定基本参数、材料、热处理、内在和表面质量等技术要求、试验方法和检验规则。
2)开发盾构机主轴承无损检测技术,制定无损检测技术规范。
3)研制内嵌式超微型传感器,开发数字化、网络化和智能化的状态监测与故障诊断软件。
4)研制盾构机主轴承试验台,考核启动摩擦力矩、最大摩擦力矩、耐久性等性能,形成盾构机主轴承试验规范。
5.3 市场需求
全球已累计生产盾构机超过10 000台,保有量达5 000多台,年需求量300~500台。目前,我国已成为世界上生产和使用盾构机最多的国家,每年需求量约400台(其中国产约300台)。另外,国内在役的盾构机约1 800余台,这些盾构机主轴承超过设计寿命后均需要维修和更换。按上述数据粗略估计,盾构机主轴承的年需求量达400套、约12亿元。
5.4 自主化
经过艰苦努力,我国已实现盾构机国产化并向国外出口,但盾构机主轴承仍全部依赖进口,主要采用ROTHE ERDE,SKF,ROBALLO,KOYO,IMO等几家公司的产品。国家科技部从2007年开始布局盾构机主轴承的国产化研发,经过十多年的努力,盾构机主轴承的研发已具备一定基础。洛阳LYC轴承有限公司与中铁隧道集团联合攻关研制的国内首套φ6.28 m盾构机主轴承已于2016年9月下线并应用于合肥地铁3号线的盾构施工,至2018年3月,经过一年多的施工应用,累计掘进里程2369.65 m,顺利完成标段工程。2019年1月14日,洛阳LYC轴承有限公司与中铁隧道集团合作研制的φ11 m盾构机主轴承下线并成功应用于舟山海底隧道的施工。2021年年初,中交天和机械设备有限公司自主研发制造的我国最大直径(16.07 m)泥水平衡盾构机“运河号”下线,其装配了洛阳轴承研究所有限公司开发的特大型管片拼装机转盘轴承。
盾构机主轴承是可靠性、安全性要求极高的产品,其自主化任重而道远,需要花真功夫,下大力气,产学研用紧密合作,积极慎重地推进盾构机主轴承的研发→工程化→产业化,最终实现自主安全可控的目标。
(参考文献略)
来源:《轴承》2022年1期(节选)
轴研所公众号 轴承杂志社公众号
营销热线
0379-64367521
0379-64880626
13693806700
0379-64886322
0379-64881181